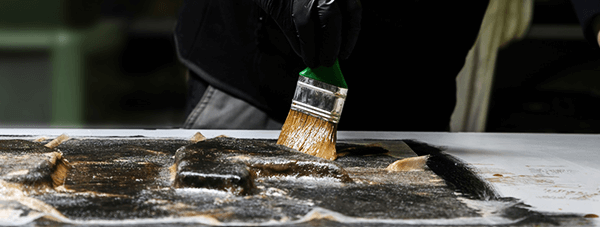
A detailed look at our composite lamination services
GRP composite lamination is more commonly used in manufacturing than metal. The increase in its usage is owed to its flexible, lightweight properties, and the fact that it can be just as strong as steel. These traits make it clear why fibreglass is the material of choice for everything from furniture, warships and supercars, to swimming pools and even structural buildings.
Creating and repairing fibreglass requires a process called lamination. To find out more, we spoke to one of Hythe Groups Technical Lead for GRP Composite Lamination, Simon Spencer.
Introducing Technical Lead Simon Spencer
With 30 years of experience, Simon Spencer is an expert composite laminator. He has been with Hythe Group for the past eight months, working within Hythe Marine Services (HMS) on fibreglass boat repairs.
Before joining Hythe Group, Simon was a composite boat builder and repair technician for the Royal National Lifeboat Institution (RNLI). Whilst Simon was with the RNLI, a friend contacted him and asked if he was interested in a four-week contract working with BAE Systems and HMS. Simon has since stayed on with HMS, completing maintenance projects on a number of Royal Naval vessels.
Simon commented, “I’ve enjoyed working with Hythe Marine Services and have a good working relationship with Josh Mathias (Managing Director of Hythe Group). I’m looking forward to staying here for the foreseeable future!”
What is GRP Composite lamination?
GRP composite lamination involves sticking individual layers of fibreglass together to create a strong material or object.
Hythe Groups head of laminating, Phill Large, explained that, “The processes involved with laminating are relatively straightforward. It involves laying layers of fibreglass material together to form strong versatile and durable sheets. You apply your 2 part resin that has been accelerated with an MEKP catalyst to your layers of dry mat material. This then needs to be hand-rolled to make sure that all air bubbles have been removed. This will then start to cure at room temperature. Once cured you have a very strong GRP (glass reinforced plastic) product.”
In the boating industry, there is a lot of wear and tear, impact and damage that can affect the integrity of fibreglass lamination. A common issue that comes with movement in boats, or just over time, is delamination.
What is fibreglass delamination?
Delamination is when some of the fibreglass layers come apart from each other, creating an air pocket inside of the object. This becomes a weak point in the lamination so composite laminators, like Simon, will grind out all of the fibreglass until they reach the delaminated layer. Once the air pocket has been removed, they will reinstate the new fibreglass to build the strength back up to the original standard.
Currently, Simon is involved with anything to do with structural repairs on Royal Naval minesweepers. A lot of the lamination projects that Simon works on are for the Ministry of Defence and are therefore protected, but they will generally follow the same process.
Firstly, a structural engineer or surveyor will evaluate the fibreglass and decide which areas are in need of repair. The laminators will then grind out the fibreglass until they reach the delaminated layer. The final step is to reinstate the layers of fibreglass so they’re compact and laminated, to ensure everything is structurally sound.
Speak with our team to discuss your next project.
How to become a GRP composite laminator
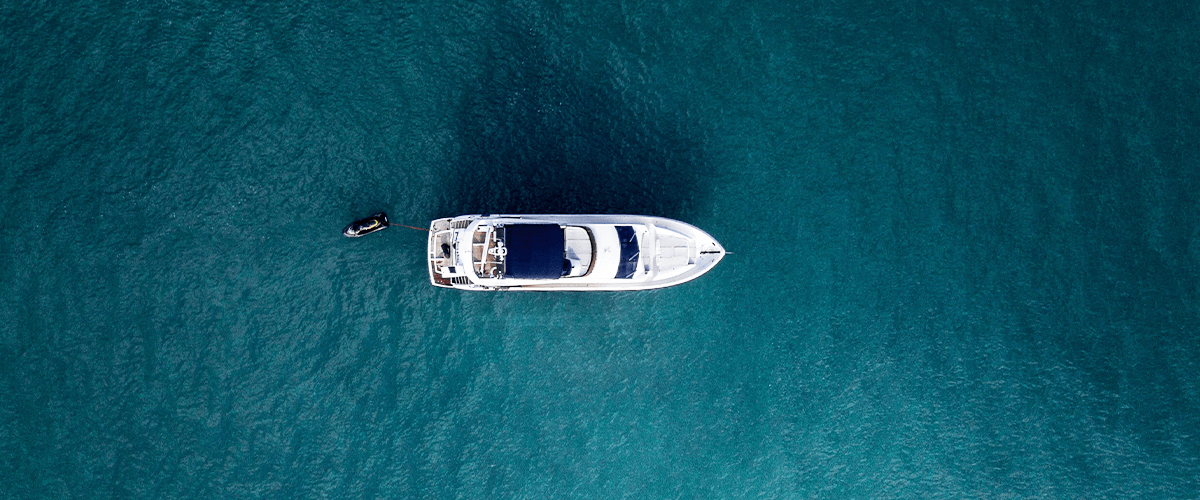
Aside from the necessary NVQ in fibreglass and lamination, the main skill of fibreglass lamination comes with experience and time-served.
Simon has had a full career of working for large international agencies but still picks up new techniques and learns more every single day. Simon told us, “Everybody has a fundamental idea of how to laminate, but the real skill comes from working in different places, watching experienced people do their job and being willing to improve.”
Laminators are continually growing their skill and knowledge to keep up with constant advancements. Composite lamination has evolved so much in the last 15-20 years, producing new methods for laminators to learn, such as fusion lamination and injection moulding.
We also spoke to Phill Large and asked what special skills laminators require. He told us, “Laminators must have a great eye for detail and an awareness of health and safety due to the dangerous chemicals that are in use. They need to be a good team player and have a methodical approach to their work.”
The challenges of GRP Composite lamination
Simon said the biggest challenge with fibreglass lamination is health and safety. Grinding fibreglass can be very harmful, so laminators must take all the necessary precautions and use full PPE protection. Every part of your body and face must be covered by overalls and a mask, and there has to be proper airflow and extraction to the working area.
Simon explained, “You might spend 2 to 3 hours getting ready to do 20 minutes of grinding. The job can be awkward and challenging, but I absolutely love it.”
Phill also described these tightly regulated conditions required to ensure the quality and safety of fibreglass lamination:
“There are many challenges in fibreglass lamination, including the conditions of working. For example, factory temperature needs to consistently remain between 16 and 25 degrees with a humidity level of under 70%. If the room is above this temperature, resins will cure too fast leaving air bubbles between your plies. If it’s too cold you will get a poor cure causing your resin to drain from the material leaving a weak component. If humidity gets above 70% this can leave moisture within your stacks, which also causes a poor cure and possibly the scrapping of your product.”
Despite these challenges, Simon commented that the job is made easier by the fact both BAE Systems and Hythe Marine Services are very experienced at what they do. “They make sure everything is done in accordance with regulations. I’ve been a laminator for so many years and this is the first place I’ve come across where you’re given the full protective uniform, hats and glasses. I’ve been with many companies and Hythe Marine are the best I’ve ever worked for.”
Working for Hythe Group
The pride Hythe Marine Services take in their employees was clear when speaking to Simon. He explained how everybody in the company, right up to the Managing Director, has excellent communication and show genuine interest by checking on you and providing regular updates. Simon told us that the working dynamic at Hythe Group goes, “above and beyond the rest”, with employees constantly being shown how much they’re valued, “With Hythe Group, once you’re through the door you’re not forgotten, that’s where they stand out from the rest.”
Hythe Groups Managing Director, Josh Mathias, said, “Our retention rate is incredibly high because we treat our workforce correctly and allow them to showcase their specialities. This builds respect within the company structure and is displayed as a finished product for the client.“
HMS, at its foundation, is an engineering company and therefore knows the high standards required to carry out projects. As a result, when offering clients one of their newer services, known as a labour only service, they are being guaranteed one of Hythes own workforce who has been vetted and, more likely than not, worked within Hythe on various projects over many years. With this type of service, customers are getting the full support of a highly capable, multi-skilled engineering company with each person that joins their self-managed team.
Josh commented, “We have built teams that work closely with our clients for many years, going as far back as our older companies Mathon & Avrotech. Within our network, we can build teams across multiple trades and quickly, mobilise and relocate them to where the work is required. If your project is in need of additional specialist support, there are not many better companies to approach. We will only ever say yes to projects when the client’s expectations can be reached. ”
To discuss how our fibreglass lamination services can help your next project contact us via the button below.