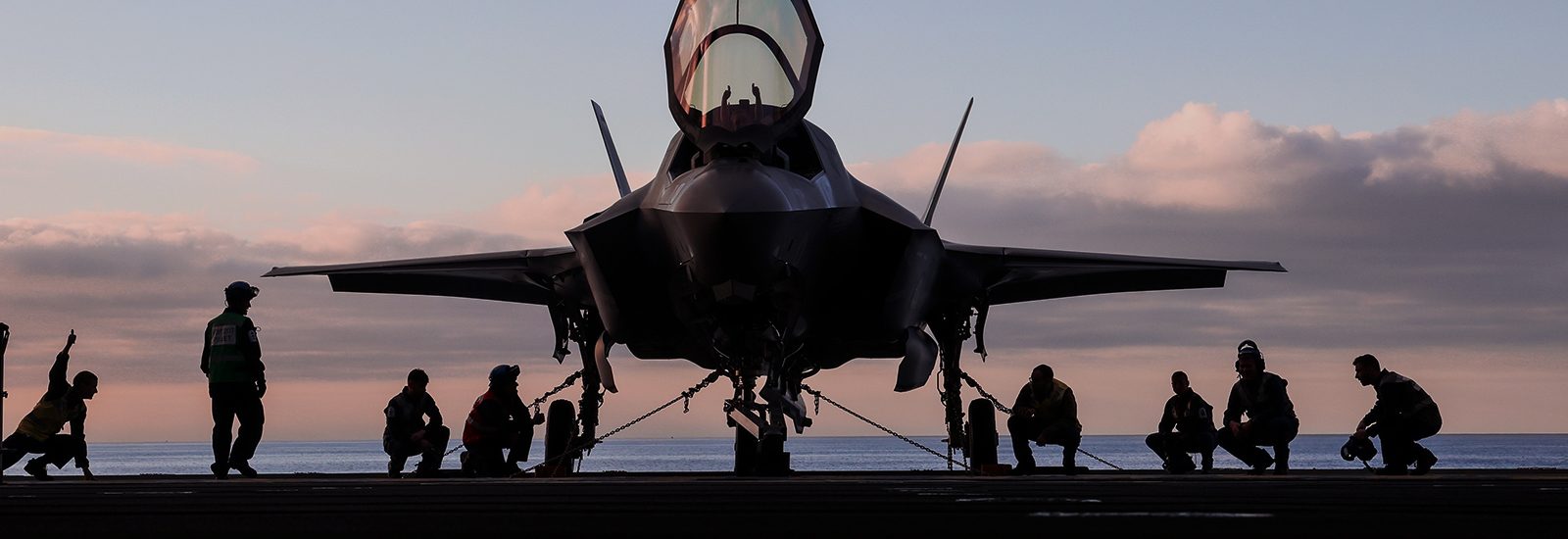
Inspecting and Maintaining Royal Naval Vessels
Sea Tube and Pump Bowl Maintenance
To ensure the highest standard of safety and performance, Royal Navy vessels periodically dock at Naval Bases for maintenance. This includes the inspection of underwater fittings and hull integrity to ensure the components are fit for service. These inspections are completed by external inspection authorities, such as Lloyds and BAE systems. When a component requires maintenance, Hythe Engineering will check its condition and carry out any required work.
We spoke to one of Hythe’s key managers, Ken Keeling, to find out about one of his current projects – Sea Tube and Pump Bowl maintenance on a T45 Royal Naval Warship.
Introducing Hythe Engineering’s Key Manager Ken Keeling
Before his role at Hythe, Ken gained experience on Naval Bases working for the Royal Navy as a Warrant Officer Marine Engineer and for BAE Systems.
Ken is a project manager on this particular Royal Naval warship maintenance project. As part of his current role, Ken is monitoring resources, timescales and value management for the project. Ken told us, “Essentially, as a Project Manager with Hythe, my main responsibilities are to monitor the project’s progress with regards to cost and time alongside other Hythe Engineering Project Managers.”
Hythe Engineering’s History of Maintaining Naval Vessels
Hythe Engineering has been maintaining Royal Naval vessels for years, allowing them to build world-renowned expertise and experience.
When Ken was working for BAE Systems he used Hythe’s services himself: “I used to use Hythe Engineering whilst working at BAE Systems, because of their ability to provide 24/7 high-quality fabrication services.”
Within this specific sea tube (or Sea Inlet) and pump bowl maintenance project, there is a whole range of Hythe Engineering services being used and numerous roles all working together. These include pipefitters, machinists, managers like Ken, and fully-trained Belzona application representatives. Also on the project are welders, Senior weld inspectors and fire-watchers to ensure the safety of the weld whilst in a compact environment. And of course, the Hythe apprentice steelworkers, pipefitters and welders are working closely with existing tradesmen, gaining valuable experience.
What is sea tube maintenance?
Sea tubes, which are more widely known as sea inlets and outlets, directly connect the services required in the ship, such as cooling water or discharge systems, to the sea. Their condition is critical to the watertight integrity of the hull, so they are key to whether or not the vessel is fit for service. High volumes of water pass in and out of these tubes at varying pressures and velocities, so they can become subject to erosion.
Sea tube maintenance involves analysing the pipe condition and exercising any necessary repair options. Hythe may perform weld repairs, apply Belzona coatings or remove the sea tube completely, replacing it with a brand-new one.
What’s unique about this work is that some repairs necessitate cutting the sea tube, where only a small section is corroded or damaged. The Hythe team will remove the damaged part and create a replacement in accordance with defence and manufacturing specifications. This will then be welded into the parent sea tube that’s still in the hull.
What is pump bowl maintenance?
A similar process to sea tube maintenance applies to pump bowls. They have routine inspections that monitor their performance, check for wear and may show that defects are arising.
Generally, a pump has rotating elements, which whilst in service can be subject to erosion and wear. When Hythe are performing maintenance, elements of the pump unit will be dismantled and worn or damaged equipment that requires repairs will be identified. The pump casing (bowl) is an example of equipment that usually requires repair. Once removed, they will blast it, clean it, and build it up with a polymer coating to bring it back to manufacturing specifications. In this project, this will be Belzona polymer coatings.
Hythe Engineering use Belzona because it’s a hard-wearing coating that adheres and bonds to metals very well. As a result, the Royal Navy doesn’t have to purchase new components as often so it’s a great cost-saving measure. With castings like pump bowls, it’s difficult to weld repair. Belzona allows restoration of the pump’s original dimensions and increases its longevity.
The challenges of working on Naval Vessels
One of the problems faced by Hythe Engineering when they are working on Naval warships is accessibility. The vast majority of the tubes are in the machinery spaces to allow cooling water to get to the various systems. When the ship is being built, the sea tubes are one of the first things to be installed. At this point, there is still plenty of space. After sea tube installation, the systems, pipework, support platforms and machinery seating are put in. The sea tubes end up being confined in very small spaces with huge access restrictions. Ken and the other Project Managers must consider the time and resources needed to strip out necessary components to give access to the sea tubes. Once the job is complete, all of these elements then need to be replaced in their correct design configuration.
Another challenge to the team is time constraints. The Naval ships docked maintenance periods vary depending on vessel class, and could be anywhere from 18 months to 6 weeks. If a sea tube needs urgent maintenance, Hythe Engineering could be called to work 24/7 depending on the severity and impact on the ship.
What’s Next for the Hythe Engineering Team?
Despite the challenges brought to the team by the current COVID-19 pandemic, they are continuing to work in support of the Royal Navy whilst respecting social distancing rules.
When asked about his upcoming projects, Ken told us, “You never know what the next project will be. We are a very reactive company. We get a shout from the customer and start to deal with it immediately. Reactive work is a large part of Hythe’s past and continues to be a requirement our customers rely on us to deliver.”
Get in touch with our team to discuss your upcoming projects.