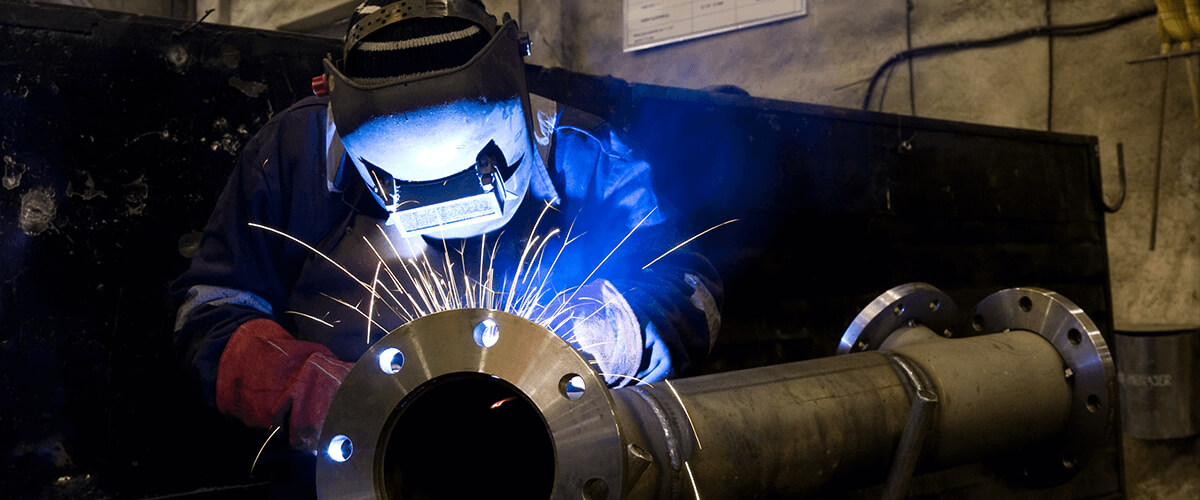
Lloyd’s Coded Welders: Why we’re different…
To ensure the highest welding standards are consistently met, all Hythe Engineering welding procedures are developed in accordance with the recognised British/ISO Standards, using Lloyd’s rules and regulations and with the aid of Lloyd’s surveyors as witnessing authorities.
Our team of Qualified Welders carry out testing against Lloyd’s code-compliant processes using various welding methods including MMA, FCAW, MIG, MAG, TIG on many different materials, like carbon steels, stainless steels, Inconel, aluminium and CuNi. The final independent review is from a surveyor, tasked by Lloyd’s Register. The review process monitors and improves the safety and quality of construction requirements for shipbuilding, marine engineering, structural steelwork (BS EN 1090) and any general welding activities.
“Lloyd’s Register Foundation is an independent global charity that helps to protect life and property at sea, on land, and in the air.” – The Lloyd’s Register
What is Lloyd’s Coded Welding?
Coded welding refers to those with official certification, whose welding work is traced and recorded to maintain the required quality standards.
“Our value lies in our experience and reputation for quality inspection. We were there as shipbuilders went from using wood to using iron and steel. Today, we inspect that steel and qualify the welders and welding procedures that fabricators use to weld safety-critical equipment and structures.” – The Lloyd’s Register Foundation
Particular to the marine industry and Hythe Engineering, the Lloyd’s Register provides the industry standard in coded welding. Originally Lloyd’s Register started out as a marine classification society in 1760. They are now a leading provider of professional services for marine engineering. The missions of Lloyd’s Register are “improving safety and increasing the performance of critical infrastructures for clients in over 75 countries worldwide.”
Within shipbuilding and maintenance, welding is one of the most critical operations. If a weld was to fail, the entire structure is at risk of being compromised. Current quality expectations of welding have never been higher and are the central factor in the rules of all ship classification societies. The Welding Institute states, “Rules for shipbuilding are all written with the expectation of achieving safe shipping, including Lloyd’s Register.”
The Importance of Coded Welding at Hythe Engineering
When manufacturing fabricated components and systems, welding certification is critical to the assurance of structural and pressure integrity. All Classification Societies, such as Lloyd’s, ABS and DNV, require welders to be properly qualified for the task in hand and to hold official certification. Lloyd’s Register requires the inspection and subsequent NDT and mechanical testing to be witnessed by an approved third party, as well as witnessing the weld procedure qualification and welding of the test piece. Hythe Engineering’s Director of Value Engineering explained the process of Lloyd’s inspection.
“We weld a test piece in our workshop as authorised by our company welding department. Lloyd’s witness the process ensuring it is welded in accordance with the given Weld procedure specification. On completion, it gets sent away for the required testing as defined in the relevant standards. When Lloyd’s confirms the test piece qualifies within the required acceptance criteria, we are given the go-ahead to be able to weld on the ship/site. Each time we do a job we are required to submit evidence that then gets sent to a third party for non-destructive testing, to prove the welding quality is in accordance with the relevant acceptance criteria.”
The official Lloyd’s Register Welding Certification Guide states, “Welding qualifications used for the construction, conversion, modification or repair of ships, other marine structures, offshore units and associated machinery which are classed or are intended for classification by Lloyd’s Register are to be manufactured, tested and inspected in accordance with the appropriate Lloyd’s Register Rules.”
We spoke to Hythe Engineering’s Senior Welding Inspector/Head of welding, to find out more about the weld test inspection process. “We carry out rigorous testing using British Standards as well as EN ISO standards. These give us the guidelines to follow when developing Weld Procedure Qualification Records or carrying out welder qualifications.”
All test pieces are visually inspected. If the piece is acceptable, the necessary NDT is carried out and mechanical testing when required. If the test piece passes, the welder qualification certificate is issued, signed and stamped by the Lloyd’s surveyor.
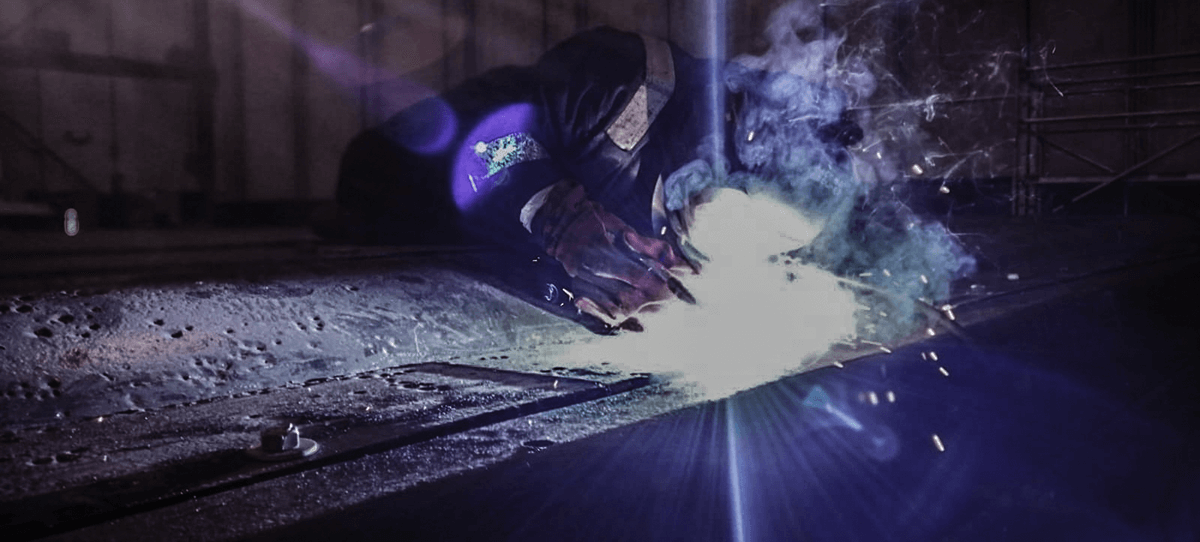
When to use Coded Welding and Welding Inspections
Hythe Engineerings’ Director of Value Engineering explained, “Not just any welder can carry out the work we do, as you must have specialist qualifications. Any of the welding undertaken on these vessels requires you to be a Lloyd’s registered welder before you’re even permitted to step onboard.”
When asked about specific projects that involve coded welding, Hythe’s weld inspector told us, “All welding carried out by Hythe Engineering involves using qualified welders and approved procedures. We can use it on not just warships for the MoD but also external customers on pipe systems or any pressure vessels or structural steelwork, which we now have accreditation for. Anything like that we will always be using qualified welders. We are very lucky here at Hythe Engineering as both our Director of Value Engineering and managing director appreciate the need to offer customers the highest quality of welding, which makes my job so much easier. Our welding department has always been backed, which means we can continually push to develop new procedures and bring in the suitable welding talent which we need. By achieving this I have found that we consistently get repeat work from customers every single day, who are pleased with the quality and also deadlines being met.”
Another priority that Hythe Engineering stipulates is that all welding is visually inspected. Throughout the company, there are inspection personnel qualified for various levels. There are Visual Welding Inspectors CSWIP 3.0 who visually inspect the external welds, and another Welding Inspector CSWIP 3.1 who deals with materials, types of materials and assess any defects they may find. Finally, there’s the Senior Welding Inspector who has the extra knowledge and experience for both internal and external welding assessment along with welding quality and increased job knowledge. We are currently in the process of allowing all of our welders to become CSWIP 3.0 visual welding inspectors. All welding apprentices will also complete this course once they have finished the first 2 years of training.
How to become a Lloyd’s Coded Welder
Achieving the status of Lloyd’s Coded Welder requires the witnessing of a successful test weld by an external examiner, surveyor or testing body. The test examines the skills of the welder and their ability to produce a weld of satisfactory quality in accordance with supplied procedures. There are limits given on flaws associated with the shape of the weld bead, such as excess weld metal and concavity, to assess the welder’s true competence and skill.
After completing a weld following Lloyd’s approved weld procedures and materials, Hythe Engineering arranged for a Lloyd’s surveyor to come in and carry out their external assessment. The Lloyd’s surveyor will witness the testing carried out by Hythe Engineering welding inspectors, to ensure everything has been completed in accordance with the official weld procedure. Once the Lloyd’s witness and Senior Welding Inspector are satisfied with the assessment, the weld is then sent away for Non-Destructive Testing (NDT).
Hythe’s weld inspector explained to us what these tests might involve. “NDT could be in the form of radiography, dye-penetrant inspection or surface crack detection.” depending on the type of weld configuration or material.
If this is all that’s required for the specific qualification, then the Senior Welding Inspector writes up the welder qualification, which is then sent off to Lloyd’s who will review, sign and stamp it. Some welded plates may require additional testing using a laboratory where mechanical testing is carried out. Unlike NDT, mechanical testing is destructive, so the test weld won’t be returned. The test plate is cut up into sections so the relevant tests can be carried out. If the weld plate is satisfactory then the Senior Welding Inspector will complete the welder qualification to be signed and stamped by Lloyd’s.
These qualifications will then be uploaded to the Hythe Engineering system where they can be circulated to customers should they need to see it. Hythe Engineering also ensures that our welders are prolongated every 6 months up to a 3 year period. Once the period has elapsed then we re-qualify them.
The Advantages of Lloyd’s Coded Welding
For Hythe Engineering, holding Lloyd’s Coded Welder status assures customers that they are meeting relevant quality standards that are recognised worldwide. He said, “The main benefit for customers is that by Hythe using Lloyd’s Coded Welding they are stating they supply a quality process. This assures customers that the standards we operate to are proven to work. The main factor is that an external surveyor comes in and makes sure we are using the right materials, that the welders are testing in the correct positions, and that we’re using the right consumables against the given weld procedure specification.”
In essence, the customer is guaranteed a process that is quality assured and can be backed up with full traceability on all materials used.
Looking for a Lloyd’s Coded Welder? Contact us.