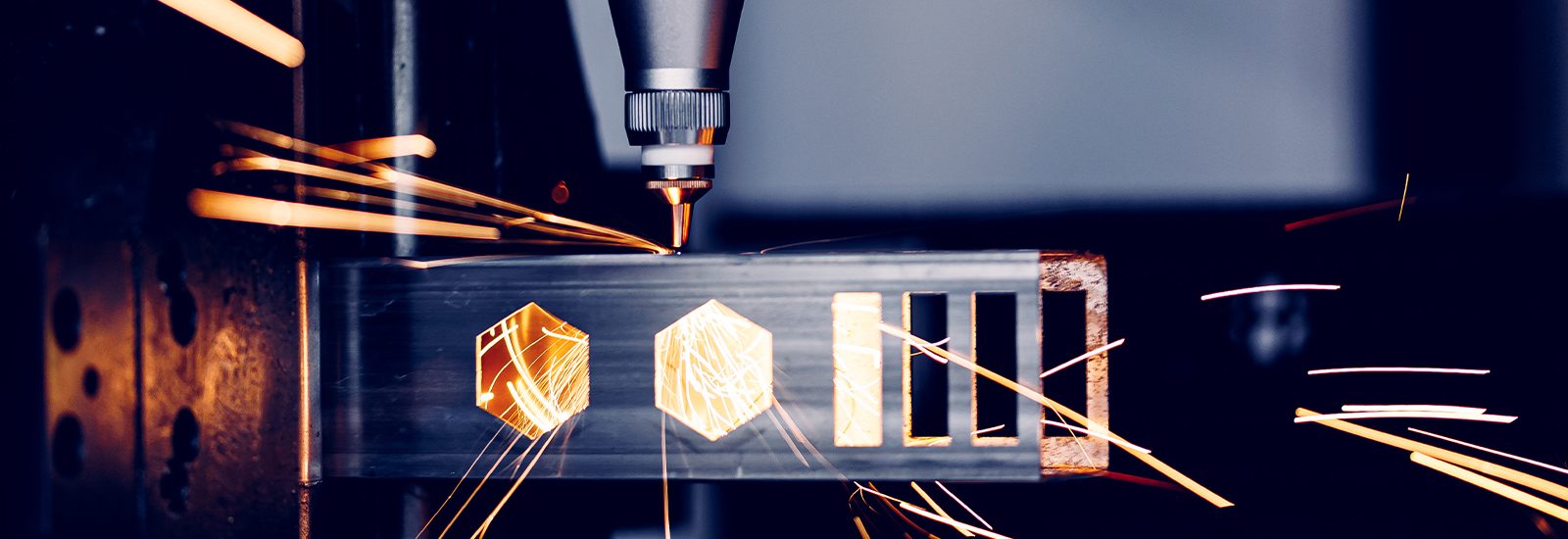
Customising CuNi Welding Procedures for Greater Performance
At Hythe Engineering, we are committed to pushing boundaries and constantly seeking ways to enhance our processes, ensuring that we deliver nothing short of the best for our clients.
With quality and process efficiency in mind, our team is embarking on a journey of innovation and improvement within our welding procedures. Recognising the need for enhanced CuNi welding in busy periods of active response work, the Hythe Team initiated a comprehensive overhaul of the existing process.
The Challenge
Even though the CuNi welding procedure is functional, it could be improved in terms of the quality and efficiency standards we strive for – especially during busy periods. The team realised the potential for improvement and undertook the task of redefining how CuNi welding was performed.
“Although we have extremely capable CuNi TIG welders, the sheer workload has led us to the possibility of bringing in another process known as Orbital TIG welding, which could certainly increase welding performance. Trials are in the very early stages and the required equipment comes at a high cost, so we still need to consider whether it’s economically viable.”
Hythe | Senior Welding Inspector
The Process
Over nine months, our team re-evaluated and re-engineered the CuNi welding procedure, investing time, effort, and resources into ensuring the process meets our higher quality expectations and efficiency goals.
While they still have a long way to go, the results of their work so far are very exciting. At present, they are working alongside a welding supplier and equipment manufacturer to see whether requirements can be met to the relevant required standards including mechanical and NDE testing. Qualifications will be to relevant British Standards and Lloyd’s Rules and regulations for Naval vessels.
Testing and development are being carried out by Hythe Engineering welding department, RH Davey Welding Supplies and Polysoude (the manufacturer of the Orbital TIG welding system). Lloyd’s Register EMEA will witness testing and approve the method and procedures.
The Outcome
If all goes well with weld testing and cost-benefit analysis, the team could expect to see a quicker turnover in the actual welding of butts. Initial set-up time for preparing materials may require more care and attention under welding procedures, but more work is being planned to improve efficiencies further down the line which may result in time and costs being kept down.
“Redefining the CuNi welding procedure showcases the impact that a focused approach to process improvement can have on elevating the overall standards of our business.”
Hythe | Senior Welding Inspector
Stay tuned for more success stories as we continue to push the limits of innovation and quality in our industry.
Contact our team
For engineering consultancy, project management and advice, please contact our team.