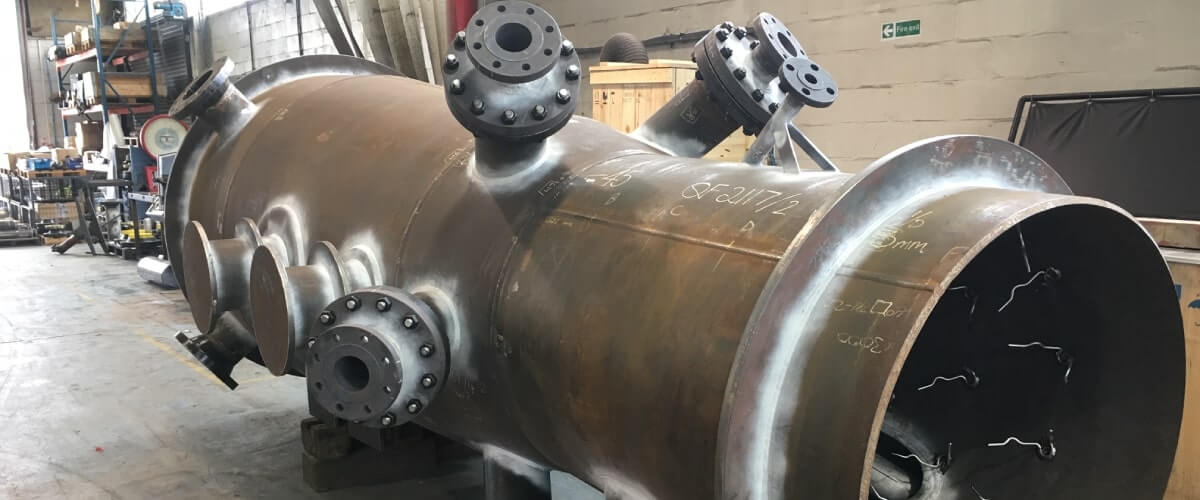
Hythe Engineering’ Expand into the UK Petrochemical Industry
Hythe Engineering is utilising its existing pipework and fabrication skills to expand into the UK Petrochemical industry. To lead the expansion, Matt Cross has joined to share his 13 years of sector knowledge and experience with the team.
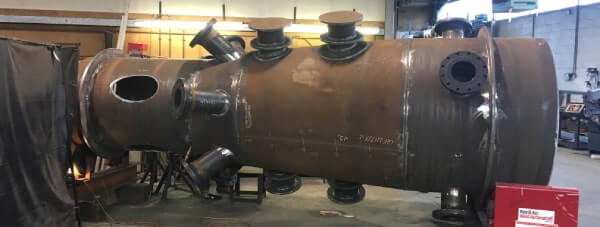
Before joining Hythe, Matt was a Mechanical Engineering Estimator and Project Manager within the oil and gas industry. In 2020, Josh Mathias, CEO of Hythe Engineering, approached Matt to help Hythe diversify into the UK Petrochemical Industry.
Matt explained, “The nice idea is that it complements the skills Hythe already have. We aren’t reinventing the wheel or anything, so it makes sense to expand. We’re taking the skills we’ve got within the group and reapplying those skills in a different sector.”
We spoke to Matt to find out about what exactly PetroChem is, his career and expertise, and how it applies to Hythe Engineering.
What Does The Petrochemical Industry Produce?
The term PetroChem, put simply, refers to the industry and process that refines oil. The petrochemical industry is the refining of oils, like crude oil, to make plastics, rubbers, petrol and diesel.Hythe Engineering will be fabricating the equipment and pipework required for the UK petrochemical industry.
Matt explained, “PetroChem is a process rather than a product, it’s a loose term to collectively cover a whole range of subjects and services, much like the travel or marine industry.”
Why are petrochemicals important?
The importance of petrochemicals is that even with global advancements in sustainable power and renewables, the world will always need oil, gas, plastics and rubber, so there will always be a consistent demand for the petrochemical industry.
What Will PetroChem Look Like at Hythe Engineering?
Expanding into the UK Petrochemical industry seems like a natural next step for Hythe, as the process of fabricating pipework for petrochemical companies is very similar to the marine industry.
Both industries largely involve pipework fabrication and installation. The main difference is that instead of working on boats, the product of Petrochem is in a petrochemical plant.
Matt told us, “Hythe will utilise the skills that we have within the Group already in the marine side, and redistribute them into a different sector.”
Once the training and initial set-up is complete, the Hythe team will be working anywhere from small gas sites to large Petrochemical plants. The Petrochem service at Hythe Group will be providing:
- Process piping fabrication
- Skid-mounted equipment
- Skid modular equipment
- Carbon and low temp carbon steel
- Stainless and alloy steel piping
When asked whether the staff will require new qualifications or retraining, Matt commented, “The skillset has the same foundation but a few paperwork exercises will be required. The oil and gas industry is largely based on American ways of working and their qualifications – whereas the marine industry is more of a British service.”
Testing and Inspection of PetroChem Services
Weld testing and weld inspection is a fundamental part of all work carried out by Hythe. In fact, anybody who completes welding activities for Hythe is undergoing training to achieve Certified Visual Weld Inspector Status.
Inside the new Petrochem department, these values of quality and rigorous testing will form the basis of all projects.
All welders and fabricators will be working to, and inspected using, CSWIP Welding Inspection standards, as well as following ASME IX Weld Procedures.
Process piping fabrication in, or for, petroleum refineries also follows ASME B31.3 Piping Fabrication requirement. This standard is designed to control quality in everything from the materials and design, to the fabrication, inspection and testing of the pipework.
Matt’s Career and Experience in the UK Petrochemical Industry
For the last 13 years, Matt has been working for a petrol chemical fabrication company. The work replicated what Hythe offers but within a different sector. Matt told us, “What you see at Hythe with the fabricators and welders, we had exactly the same service. Instead of putting it on boats, we were putting it in oil refineries and buildings.”
Matt is skilled in quotations, pipework, process pipework fabrication engineering and skid manufacture. He started his career as a Fabricator Welder Apprentice, much like many of the team at Hythe.
Matt then moved from the shop floor to work as an Estimator for the company, before working his way up through the ranks to become a Senior Estimator and Senior Project Manager. They were a small firm, so Matt was involved in everything from procurement, and quality management, to estimation. Matt said, “Even though we had titles of Senior Estimator or Senior Project Manager it was a very varied role.”
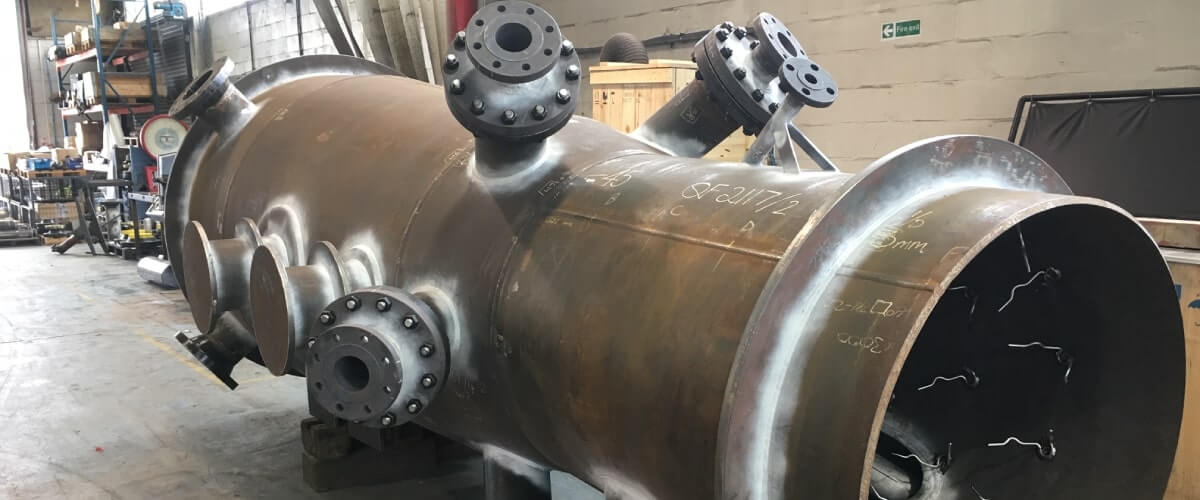
Examples of Matt’s Past Projects
Project Managing two FCCU Injections Sections and Associated PAU’s:
Matt Project Managed the estimation, procurement, fabrication, testing, refractory lining and delivery of two new FCCU injections sections and associated PAU’s (Pre-assembled Units).
This project consisted of the two new sections being SA516 Gr 70 rolled shells with multiple penetrating nozzles in carbon, stainless and exotic steels, 5” refractory lined and with thermally sprayed aluminium external coating.
Associated with the riser section, were six number PAU’s made up from BS EN 1090 structural steel, ASME B31.3 process piping fabrication.
This project involved overseeing multiple subcontracts to ensure the project was delivered on time to meet with the clients shut down.
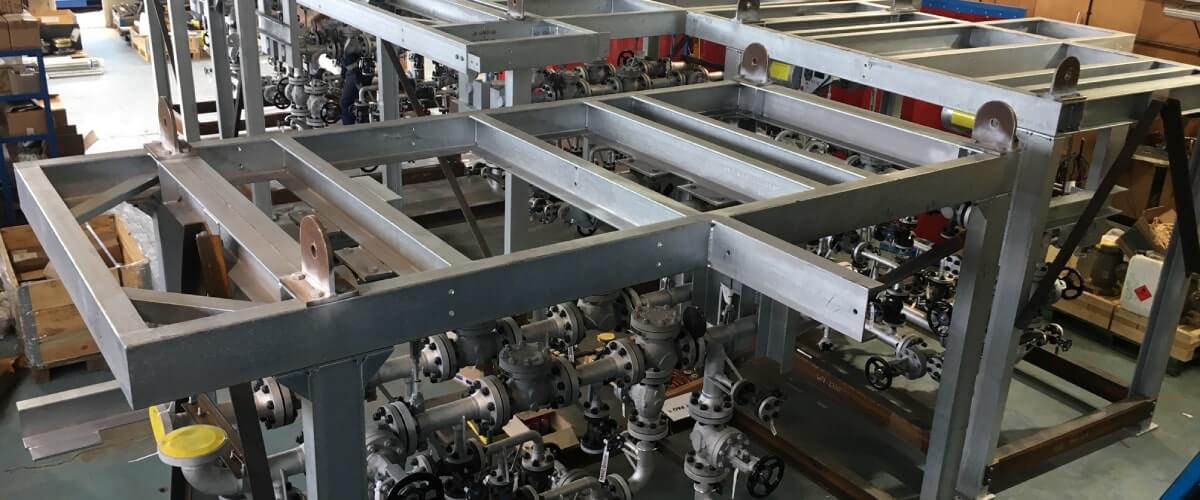
Developing Bespoke Solutions:
Matt worked with a client on a project for enabling works within their saltwater security system, to allow for the future devolvement of the site.
A bespoke solution was developed with the client’s engineers to meet the scope requirements. This project involved splitting a 48” fire main line into three 20” lines within a restricted space.
The project required a range of materials, including super duplex as well as multiple of surface finishes.
Click here to speak with Matt about Petrochem and pipework fabrication services.